The term "Jacobs Ladder" can evoke a variety of images, from a biblical stairway to a specific type of body modification. However, in the intricate world of blades and craftsmanship, "Jacobs Ladder" has also become synonymous with a particular lineage of knives, often sparking curiosity and debate among collectors and enthusiasts. This article delves deep into the fascinating story of Jacobs Ladder knives, exploring their origins, the family behind them, their perceived value, and the broader context of knife making and collecting. While some might encounter the phrase "jacobs ladder pericing" and wonder about its connection to body art, our focus here is squarely on the unique and sometimes controversial knives that bear this intriguing name, as revealed by insights from those directly involved in their creation and legacy.
Understanding the narrative surrounding Jacobs Ladder knives requires a look at the claims, counter-claims, and the sheer passion that defines the knife community. From discussions about their utility and design to the economics of their pricing and the ethics of their production, these knives offer a compelling case study in the nuances of the custom knife market. Join us as we cut through the speculation to uncover the truth behind Jacobs Ladder knives, providing a comprehensive guide for anyone interested in their history, craftsmanship, and place in the broader world of edged tools.
Table of Contents
- The Jacobs Ladder Enigma: Defining the Knives
- A Family's Craft: The Jacobs Legacy in Knife Making
- Beyond the Blade: Understanding Knife Utility and Design
- The Signature of Authenticity: Marking and Personalizing Blades
- The Economics of Edges: Valuing Custom and Heirloom Knives
- Inside the Workshop: Tools and Techniques of Knife Craft
- Navigating the Knife Market: Insights for Buyers and Sellers
- Upholding Standards: Ethics and Trust in the Knife Industry
The Jacobs Ladder Enigma: Defining the Knives
The name "Jacobs Ladder knives" itself carries an air of mystique, a label often applied by the community rather than a formal brand designation. These knives have been a subject of discussion within online forums and among collectors for years, with conversations often revolving around their origin, quality, and the business practices associated with them. The phrase "I have heard these knives called 'jacobs ladder' knives" highlights this informal nomenclature, suggesting a community-driven identification rather than a manufacturer's label. This collective naming indicates a shared understanding among enthusiasts about a particular type or lineage of blades. Initially, the perception of these knives was sometimes clouded by claims that they were simply "cheap knives, restamping and reselling for a long time." This assertion, if true, would raise questions about authenticity and value. The idea of acquiring a knife under such circumstances, particularly when one is "much younger, and uneducated about knives," points to a common experience for many budding collectors. The allure of a unique or custom-looking blade can often overshadow a deeper investigation into its provenance. Understanding the "Jacobs Ladder" identity, therefore, means navigating these various perspectives, from those who view them with skepticism to those who appreciate them for what they are. It’s a crucial first step in comprehending their place in the diverse world of edged tools.A Family's Craft: The Jacobs Legacy in Knife Making
At the heart of the "Jacobs Ladder knives" discussion lies the Jacobs family, whose involvement in knife making and distribution has been a long-standing tradition. The narrative shifts significantly with the direct intervention of a family member, Joshua Jacobs, who stepped forward to clarify misconceptions and verify their operations. This personal testimony is vital for understanding the true nature of these knives and the family's commitment to their craft. The statement, "Because of a post from 13 years ago continuing to get circulation, i'd like to explain that i am joshua jacobs, the son of jason jacobs," provides a direct link to the family behind the knives. It's a testament to the enduring nature of online discussions and the need for accurate information. Joshua's willingness to engage with the community and address historical claims head-on adds a layer of transparency and authority to the discussion surrounding Jacobs Ladder knives.Joshua Jacobs: Setting the Record Straight
Joshua Jacobs's declaration, "I can and will verify that we make knives," is a pivotal point in the ongoing dialogue. This direct confirmation counters any lingering doubts about the family's active role in the manufacturing process. It shifts the perception from mere "re-stamping" to genuine production, albeit potentially alongside other business models. This verification is crucial for establishing trust and credibility within the knife community, where authenticity and craftsmanship are highly valued. The family's long history in the business, even if it involved "buying cheap knives, restamping and reselling for a long time" in earlier phases, suggests an evolution in their practices. It's common for businesses, especially in artisanal fields, to adapt their models over time. Joshua's clarification indicates a desire to present the current reality of their operations, emphasizing their legitimate knife-making endeavors. This insight into the Jacobs family's direct involvement is fundamental to understanding the "Jacobs Ladder" phenomenon beyond simple rumors and anecdotes.Beyond the Blade: Understanding Knife Utility and Design
The functionality and design of Jacobs Ladder knives have been subjects of considerable debate among enthusiasts. While some knives are celebrated for their practical utility and robust construction, others, including certain Jacobs Ladder blades, have been perceived differently. This distinction often lies in the intended purpose and the inherent design philosophy behind the knife. The observation that these knives are "overall fun to play with but imho mostly a toy" speaks volumes about their perceived utility. This doesn't necessarily diminish their appeal but places them in a category distinct from tools designed for heavy-duty tasks or self-defense. The "fun to play with" aspect suggests an appeal rooted in novelty, collection, or casual use, rather than demanding practical applications. This perspective is crucial for setting realistic expectations for potential owners of Jacobs Ladder knives.The "Toy" Versus "Tool" Debate: Jacobs Ladder Knives vs. Balisongs
To further illustrate the functional distinction, the comparison to a balisong is particularly insightful: "Unlike a balisong which is a great practical design." A balisong, or butterfly knife, while often associated with recreational flipping, is fundamentally a tool with a robust and practical design for opening and closing, and when well-made, can be a highly effective cutting instrument. This comparison highlights a perceived lack of practical design in some Jacobs Ladder knives, positioning them more as collectibles or recreational items rather than everyday carry tools. This debate underscores a broader point in the knife community: the difference between a knife designed primarily for aesthetic appeal or casual handling and one built for demanding tasks. While a knife can be both beautiful and functional, the "toy" label often implies a compromise on durability, edge retention, or ergonomic design for practical use. Understanding where Jacobs Ladder knives fall on this spectrum is key for collectors and users to appreciate them for their true qualities and limitations. It's a reminder that not all knives are created equal in terms of their intended utility, and a "fun" knife can still hold significant value for the right enthusiast.The Signature of Authenticity: Marking and Personalizing Blades
In the world of custom and artisanal knives, a signature on the blade is more than just a mark; it's a testament to authenticity, craftsmanship, and the maker's pride. For Jacobs Ladder knives, the presence of a signature can be a key identifier, prompting questions from collectors about its application. "Ok so ive seen some pictures with a signature on the knife blade and i was wondering how this is done" reflects this common curiosity. The signature transforms a generic blade into a piece attributed to a specific artisan or workshop, adding to its provenance and potential value. The method of applying a signature to a knife blade varies, depending on the maker's preference, the material of the blade, and the desired aesthetic. Common techniques include etching, engraving, stamping, or even laser marking. Each method requires specific tools and a degree of skill to execute cleanly and permanently. The signature serves as a unique fingerprint, distinguishing a custom piece from mass-produced items and often indicating the quality and care invested in its creation.Essential Tools for Blade Engraving and Customization
For aspiring knife makers or those interested in personalizing their blades, understanding the "tool and equipment do i need to write my signature on the blade" is essential. The choice of tools depends heavily on the desired outcome:- Electrochemical Etching Kits: These are popular for their ease of use and ability to create dark, permanent marks without removing much material. They use an electrical current and an electrolyte solution to etch a design through a stencil.
- Vibratory Engravers: Handheld tools that use a vibrating tip to scratch designs onto the surface. They are versatile for freehand work but may not produce as deep or crisp a mark as other methods.
- Laser Engravers: Offer high precision and speed, capable of intricate designs and consistent results. However, they represent a significant investment and require specialized knowledge to operate.
- Hand Engraving Tools (Gravers): For traditional craftsmanship, skilled artisans use various shaped gravers to hand-cut designs into the metal. This method requires immense skill and patience but yields beautiful, tactile results.
- Stamping Dies: For repetitive marking, custom-made steel stamps can be used to impress a signature or logo into the blade, typically before heat treatment.
The Economics of Edges: Valuing Custom and Heirloom Knives
The valuation of knives, particularly custom and heirloom pieces, is a nuanced process that goes far beyond the cost of materials and labor. As someone "just beginning this journey, i have some questions regarding the pricing of custom knives, particularly fixed blade," highlights a common challenge for new collectors and makers alike. The principle of "Economics 101 dictates that something is worth" what someone is willing to pay for it, but this seemingly simple truth is influenced by a myriad of factors in the knife market. For custom knives, factors influencing price include the maker's reputation, the complexity of the design, the quality and rarity of materials used (e.g., exotic steels, handle materials like mammoth ivory or stabilized wood), the level of finish, and the overall craftsmanship. A fixed blade knife, for instance, might command a higher price due to its inherent strength and often more intricate grind lines compared to a folder. The story behind the knife, its unique features, and the demand for the maker's work all contribute to its market value.Preserving History: The Art of Heirloom Knife Restoration
Heirloom knives introduce another layer of complexity to valuation, where sentimental and historical value often supersede mere monetary worth. The desire to "repair/restore an heirloom remington r1123 pocketknife" speaks to the deep personal connection owners have with these objects. An heirloom, even if in "fairly rough condition," can be "a pretty valuable knife" not just for its brand or original quality, but for the stories it carries and its link to family history. Restoring an heirloom knife involves delicate work, balancing the preservation of its original character with necessary repairs to make it functional or aesthetically pleasing again. This often requires specialized skills from an "oregon knifemaker" or a restorer experienced with vintage blades. The cost of restoration can be significant, reflecting the expertise required to handle delicate materials, match historical finishes, and meticulously bring the knife back to life without destroying its historical integrity. The decision to restore is often driven by a desire to honor the past and ensure the knife can continue its journey for future generations, making it an investment in heritage rather than just an object.Inside the Workshop: Tools and Techniques of Knife Craft
The creation and repair of knives, whether they are Jacobs Ladder knives or custom fixed blades, rely heavily on a specific set of tools and a deep understanding of metalworking techniques. The mention of "chucks in the last 6 months, both were 17 and neither of them had the key hole for the drift key," and "The arbor was part of the spindle so be careful," offers a glimpse into the practical realities and challenges faced by knife makers and repair specialists. These are not casual observations but details that speak to the specific machinery used in a knife-making workshop. Chucks, arbors, and spindles are components typically found in lathes or milling machines, crucial for shaping, grinding, and polishing knife blades and handles. A chuck holds the workpiece (like a blade blank or handle material) securely, while the arbor is a shaft that connects the chuck to the spindle, which rotates. The absence of a keyhole for a drift key in a chuck can indicate a keyless chuck or a design that requires different methods for removal or tightening, potentially complicating tool changes or maintenance. This level of detail highlights the technical expertise required in knife crafting, where precision and the right equipment are paramount for achieving high-quality results. Beyond these specific components, a well-equipped knife workshop typically includes:- Grinders and Sanders: Essential for shaping the blade, establishing bevels, and achieving a fine finish.
- Heat Treatment Equipment: Furnaces or kilns are critical for hardening and tempering steel, which gives the blade its strength and edge retention.
- Anvils and Hammers: Forging and shaping metal, particularly in traditional knife making.
- Vises and Clamps: For securing workpieces during various stages of production.
- Measuring Tools: Calipers, micrometers, and angle gauges ensure precision in dimensions and geometry.
- Sharpening Systems: To give the blade its final, keen edge.
Navigating the Knife Market: Insights for Buyers and Sellers
The market for knives, encompassing everything from mass-produced utility blades to bespoke custom pieces and historical heirlooms, is a dynamic and multifaceted environment. For both buyers and sellers, understanding its nuances is key to making informed decisions, especially when dealing with items like Jacobs Ladder knives or valuable collectibles. The principle that "Economics 101 dictates that something is worth" what the market will bear is particularly evident here. For buyers, navigating this market means researching the maker's reputation, understanding the materials and construction methods, and assessing the knife's condition. For custom knives, establishing direct communication with the maker can provide invaluable insights into their process and philosophy. When considering a Jacobs Ladder knife, understanding the family's history and their current production methods, as clarified by Joshua Jacobs, becomes essential for an informed purchase. Buyers should also be aware of the "toy" versus "tool" perception to align their expectations with the knife's intended utility. Sellers, on the other hand, must accurately assess their knife's value based on its rarity, condition, maker, and current market demand. For an heirloom piece like the "remington r1123 pocketknife" in "fairly rough condition," the decision to restore versus sell as-is can significantly impact its market appeal and price. High-quality photographs, detailed descriptions, and transparent communication about the knife's history and any imperfections are crucial for attracting serious buyers. The online marketplace, while vast, requires sellers to build trust and demonstrate expertise to command fair prices for their blades. Understanding these market dynamics ensures that both transactions involving Jacobs Ladder knives and other blades are equitable and satisfying for all parties.Upholding Standards: Ethics and Trust in the Knife Industry
The knife industry, like any other specialized field, operates on a foundation of trust, integrity, and ethical conduct. Discussions surrounding "Jacobs Ladder knives" and claims of "buying cheap knives, restamping and reselling" underscore the importance of these principles. For consumers, the ability to trust a maker's claims about their product's origin, materials, and craftsmanship is paramount. Ethical considerations in knife making and sales include:- Transparency: Makers and sellers should be upfront about their production methods, materials used, and any historical claims. Joshua Jacobs's effort to "set the record straight" about the Jacobs family's knife-making operations is a prime example of such transparency.
- Accurate Representation: Knives should be described accurately, without exaggerating their utility or historical significance. Labeling a knife as a "toy" versus a "practical design" is an important distinction that should be honestly communicated.
- Fair Pricing: Pricing should reflect the true value of the knife, considering materials, labor, skill, and market demand, without exploiting a buyer's lack of knowledge.
- Respect for Intellectual Property: Avoiding unauthorized reproduction or "re-stamping" of other makers' designs or logos is crucial for maintaining industry integrity.
- Safety: Ensuring that knives are safely constructed and fit for their intended purpose, with clear warnings if they are primarily decorative or recreational.
Conclusion
The journey through the world of Jacobs Ladder knives reveals a rich tapestry of craftsmanship, family legacy, market dynamics, and community dialogue. From the initial confusion surrounding their name and origin to the direct clarifications from the Jacobs family, these knives embody many of the complexities inherent in the custom and collectible knife market. We've explored the debate over their utility, the art of blade personalization, the intricate economics of valuing custom and heirloom pieces, and the essential tools that bring these blades to life. Ultimately, Jacobs Ladder knives stand as a testament to the diverse and passionate world of knife collecting. Whether viewed as functional tools, unique collectibles, or simply "fun to play with," their story is deeply intertwined with the individuals who make and cherish them. We encourage you to delve deeper into the world of knives, perhaps by exploring the work of other custom makers, learning about knife restoration, or even considering the tools needed to craft your own blade. Share your thoughts on Jacobs Ladder knives or your experiences with custom blades in the comments below, and continue your exploration of this fascinating craft by browsing other articles on our site.Related Resources:
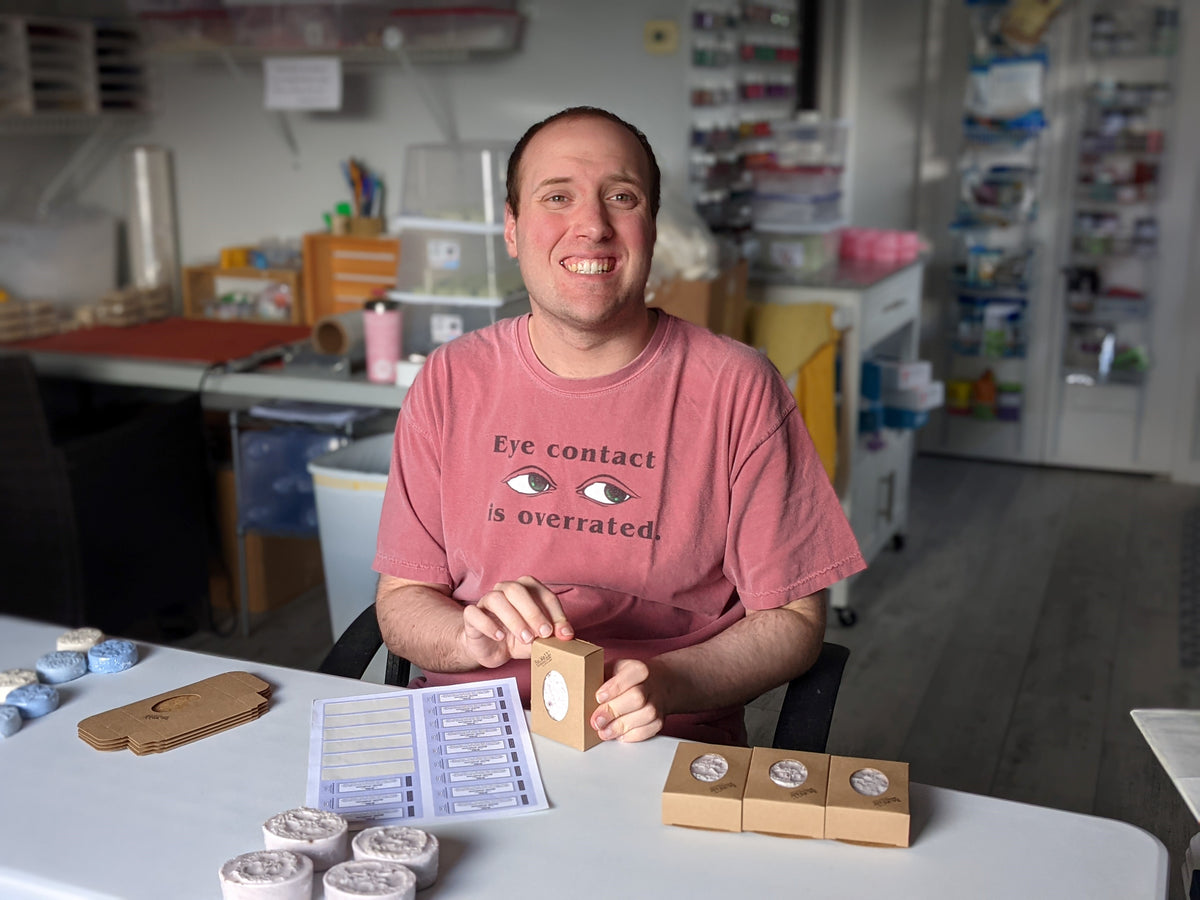
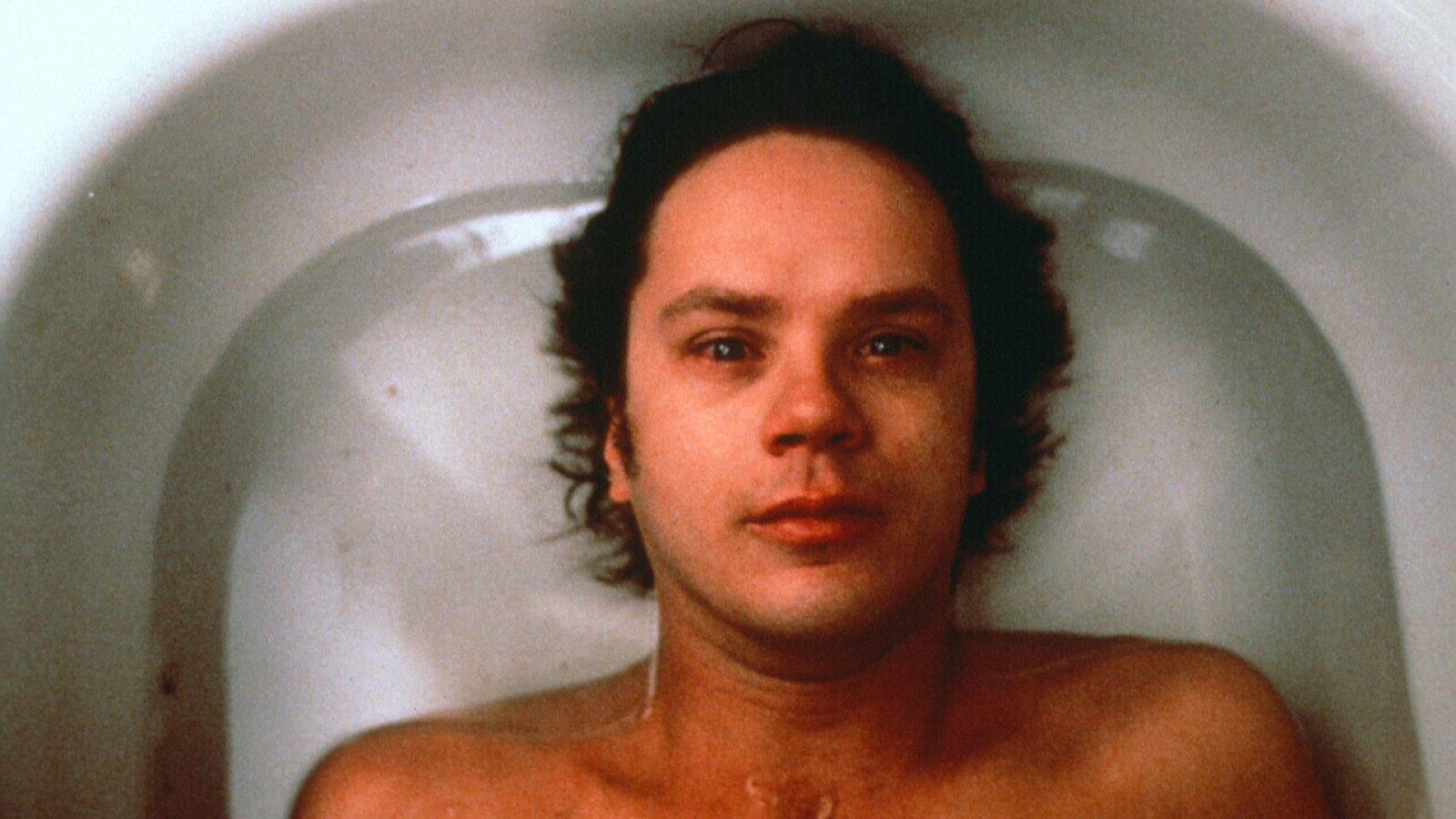
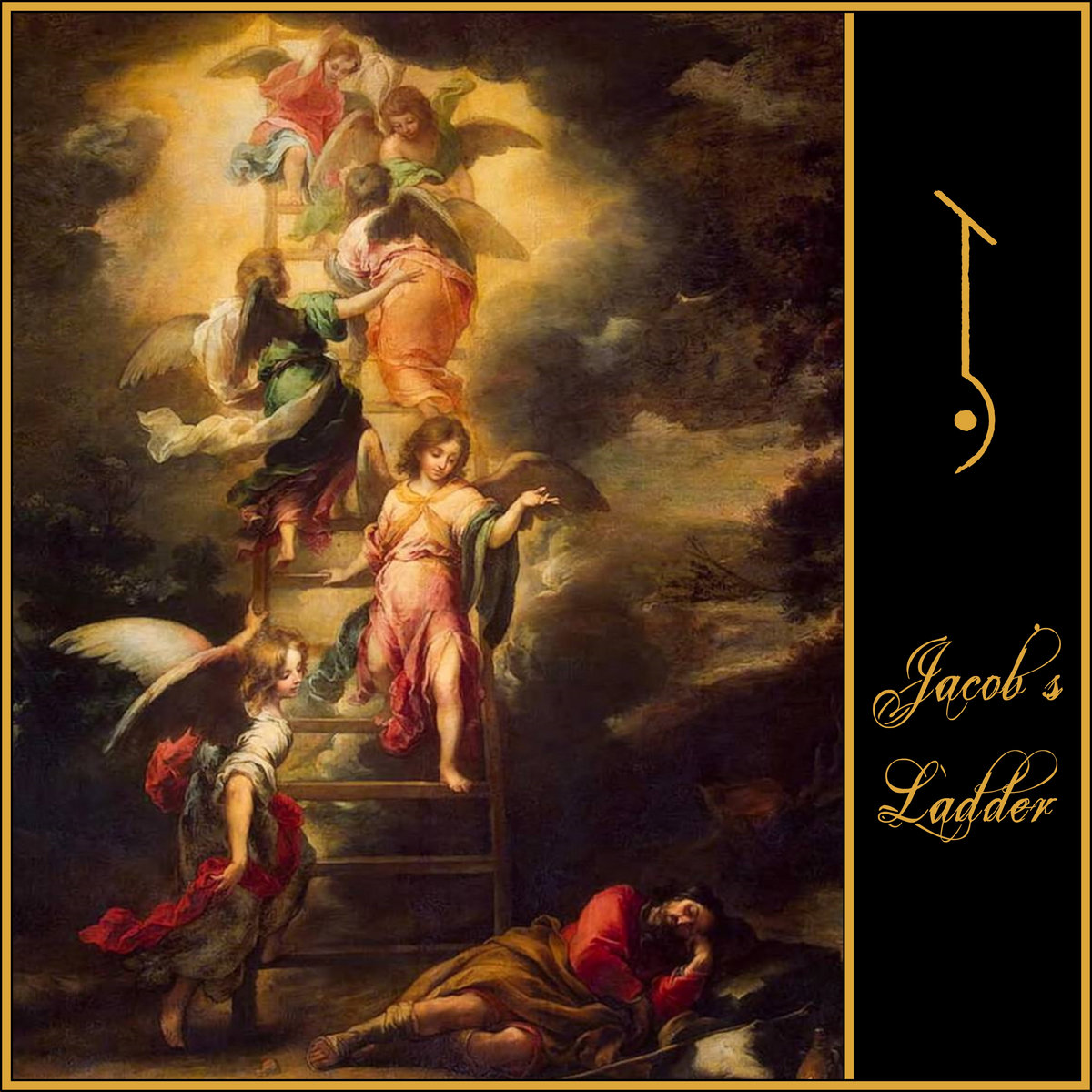
Detail Author:
- Name : Prof. Gilberto Funk PhD
- Username : emmerich.foster
- Email : korbin58@olson.com
- Birthdate : 1985-06-03
- Address : 196 Greyson Spur Apt. 637 Sydneyborough, KS 19973
- Phone : (283) 838-4776
- Company : Goodwin Ltd
- Job : Grinding Machine Operator
- Bio : Occaecati omnis quia perspiciatis placeat occaecati quo. Animi sunt ipsam natus molestias ipsam molestiae illo iste. Vel et unde saepe impedit voluptas occaecati. Iure provident rerum ullam incidunt.
Socials
twitter:
- url : https://twitter.com/cbergstrom
- username : cbergstrom
- bio : Quibusdam nobis in exercitationem possimus enim quisquam. Voluptatem laudantium pariatur qui pariatur unde.
- followers : 889
- following : 2755
linkedin:
- url : https://linkedin.com/in/bergstrom1987
- username : bergstrom1987
- bio : Enim tenetur quo non minima qui.
- followers : 937
- following : 1222
tiktok:
- url : https://tiktok.com/@claudie_bergstrom
- username : claudie_bergstrom
- bio : Qui natus dolores voluptatem maxime. Omnis dolores earum non officia.
- followers : 3782
- following : 906
facebook:
- url : https://facebook.com/claudie_bergstrom
- username : claudie_bergstrom
- bio : Necessitatibus voluptatem quia totam vel quaerat.
- followers : 2469
- following : 2930