The world of custom knives is as intricate and fascinating as the blades themselves, often steeped in family legacies and unique craftsmanship. While the term "Jacobs Ladder" might conjure images of celestial pathways or even certain body modifications, in the realm of sharp edges and fine steel, it refers to a distinct lineage of blades associated with the Jacobs family. This article delves deep into the story of these intriguing "Jacobs Ladder knives," exploring their origins, their place in the knife community, and the broader aspects of blade craftsmanship, valuation, and care.
From the personal anecdotes of a knifemaker's son to the practicalities of blade personalization and the intricate economics of custom knife pricing, we'll uncover what makes these knives, and the art of knifemaking in general, so captivating. Join us as we navigate the nuances of collecting, restoring, and truly appreciating the artistry behind every handcrafted blade.
Table of Contents
- The Jacobs Legacy: A Family Affair in Knife Making
- Understanding "Jacobs Ladder Knives": More Than Just a Toy?
- The Art of Acquisition: Buying and Reselling Blades
- The Signature Touch: Personalizing Your Blade
- Precision and Maintenance: The Mechanics of Knifemaking
- Valuing Blades: The Economics of Custom and Heirloom Knives
- Navigating the Knife Market: Tips for Collectors and Enthusiasts
- The Enduring Appeal of Handcrafted Blades
The Jacobs Legacy: A Family Affair in Knife Making
In the vast and often misunderstood world of custom knives, family names carry significant weight. For many years, a particular narrative circulated online, sometimes causing confusion or misrepresentation regarding certain blades. However, a clear voice has emerged to set the record straight: Joshua Jacobs, the son of Jason Jacobs, a prominent figure in the knife community.
- Maegan Hall Twitter
- Iwdominate Twitter
- Kennedy Jaye Onlyfans
- Grace Charis Leaked Twitter
- Ebony Twitter Videos
Joshua recently addressed this directly, stating, "Because of a post from 13 years ago continuing to get circulation, I'd like to explain that I am Joshua Jacobs, the son of Jason Jacobs." This clarification is vital, as it firmly establishes the lineage and authenticity behind the knives associated with their name. He further affirms, "I can and will verify that we make knives." This statement isn't just a claim; it's a testament to a long-standing tradition of craftsmanship and dedication that defines the Jacobs family's contribution to the art of blade making. Their work extends beyond mere production; it's about upholding a legacy of quality and design that has resonated with collectors and enthusiasts for decades.
Joshua Jacobs: A Glimpse into the Man Behind the Blade
While specific biographical details about Joshua Jacobs beyond his role as a knifemaker and son of Jason Jacobs are not widely publicized, his candid statements offer a window into his dedication to his family's craft. His willingness to address long-standing online discussions underscores a commitment to transparency and authenticity within the knife community.
Attribute | Detail |
---|---|
Name | Joshua Jacobs |
Family Relation | Son of Jason Jacobs |
Profession | Knifemaker |
Known For | Contributing to the legacy of "Jacobs Ladder knives" and other family blades. |
Community Role | Clarifying information and upholding family reputation in the knife community. |
Understanding "Jacobs Ladder Knives": More Than Just a Toy?
The name "Jacobs Ladder knives" has a certain mystique, and Joshua Jacobs himself acknowledges this, stating, "I have heard these knives called “Jacobs Ladder” knives." This nomenclature likely stems from the family name being associated with a distinctive style or perhaps a specific series of knives that gained popularity. However, the perception of these knives within the broader community can vary widely.
Joshua offers an interesting perspective on their utility: "They are overall fun to play with but imho mostly a toy." This candid assessment highlights a crucial distinction in the knife world: the difference between a collectible, a novelty, and a practical tool. While "Jacobs Ladder knives" might be appreciated for their aesthetic appeal, unique design, or simply the joy of handling them, their primary purpose might not be heavy-duty utility. This contrasts sharply with designs celebrated for their functional superiority, as he points out: "Unlike a balisong which is a great practical design." A balisong, or butterfly knife, despite its often-misunderstood reputation, is renowned for its quick deployment and robust locking mechanism, making it a highly practical tool in the hands of a skilled user.
This distinction doesn't diminish the value of "Jacobs Ladder knives." Instead, it helps collectors and enthusiasts understand their place. They might be prized for their collectibility, their unique aesthetic, or simply as a piece of the Jacobs family's history in knifemaking. Their "toy-like" quality might even contribute to their appeal for those who enjoy the tactile experience of handling a well-crafted object, rather than solely focusing on its utilitarian function.
The Art of Acquisition: Buying and Reselling Blades
The knife market is dynamic, encompassing everything from bespoke, handcrafted masterpieces to mass-produced utility tools. Within this spectrum, there's a long-standing practice of acquiring, refurbishing, and reselling knives, a practice not uncommon in many artisan crafts. Joshua Jacobs touches upon this aspect of the family business: "Jacobs has been buying cheap knives, restamping and reselling for a long time." This isn't necessarily a clandestine operation but rather a facet of the trade that allows makers to offer more accessible options or to apply their expertise to existing blades, giving them a new life and a distinctive touch.
This practice highlights the entrepreneurial spirit within the knifemaking community. It allows for the transformation of an ordinary knife into something with added value, whether through improved aesthetics, enhanced ergonomics, or the prestige of a known maker's mark. It's a way to democratize access to custom-like knives, making them available to a wider audience who might not be able to afford a fully custom, from-scratch piece.
Joshua's personal experience further illustrates the impact of such practices on consumers: "Back when I was much younger, and uneducated about knives, I bought one of his skinners at a." This anecdote resonates with many collectors who, early in their journey, might have acquired knives without full knowledge of their provenance or the nuances of the market. It underscores the importance of education for buyers, encouraging them to research makers, understand different types of knives, and recognize the value proposition of various offerings. This experience likely shaped Joshua's current understanding and his commitment to transparency within his family's business.
The Signature Touch: Personalizing Your Blade
A maker's signature on a blade is more than just an identifying mark; it's a testament to authenticity, craftsmanship, and pride. For collectors, a signed blade often holds greater value and provides a direct connection to the artisan. The question of how these signatures are applied is a common one among aspiring knifemakers and curious enthusiasts. Joshua's insights touch upon this directly: "Ok so I've seen some pictures with a signature on the knife blade and I was wondering how this is done." This curiosity is natural, as the clean, precise lines of a signature on hardened steel can seem almost magical.
The process involves specialized tools and techniques. As the query continues, "What tool and equipment do I need to write my signature on the blade," it points to the practical aspects of blade personalization. There are several methods commonly employed by knifemakers:
Essential Tools for Blade Personalization
- Electro-chemical Etching: This is one of the most popular methods. It involves creating a stencil of the signature (often using a stencil printer or vinyl cutter), applying it to the blade, and then using an etching machine (which applies a mild electrical current and an electrolyte solution) to permanently mark the exposed steel. The result is a clean, dark, and durable mark.
- Laser Engraving: For high precision and intricate designs, laser engraving machines are used. These machines use a focused laser beam to ablate or discolor the surface of the metal, creating the signature. While highly effective, the equipment can be a significant investment.
- Hand Engraving: The traditional method, involving specialized gravers (small chisels) and a steady hand. This method produces a unique, artistic mark, but requires considerable skill and practice.
- Stamp Marking: For simpler, often stylized logos or maker's marks, a custom-made steel stamp can be used. The stamp is struck with a hammer onto the blade, leaving an impression. This is best done before heat treatment when the steel is softer.
- Vibratory Engravers: Similar to a Dremel tool with a specialized engraving bit, these tools vibrate rapidly to scratch the surface. While less precise than etching or laser, they are more accessible for beginners.
Each method offers different aesthetic results and requires varying levels of investment and skill. The choice often depends on the maker's preference, the type of steel, and the desired look of the signature on the Jacobs Ladder knives or any other custom blade.
Precision and Maintenance: The Mechanics of Knifemaking
Beyond the artistic flair of design and signature, knifemaking is a highly technical craft that demands precision, specialized machinery, and meticulous maintenance. The workshop of a knifemaker is often filled with a variety of tools, from grinders and belt sanders to drill presses and heat-treating ovens. The reliability and accuracy of these tools are paramount to producing high-quality blades, including the distinct "Jacobs Ladder knives."
A common component in many workshops, particularly for drilling or grinding, is the chuck – a clamping device used to hold tools or workpieces. The wear and tear on such equipment can be significant, as evidenced by a knifemaker's practical experience: "I've replaced both of my chucks in the last 6 months, both were 17 and neither of them had the key hole for the drift key." This detail highlights the constant need for equipment upkeep. A chuck without a keyhole for a drift key can be challenging to remove, indicating a design or wear issue that necessitates replacement for continued operational efficiency.
Furthermore, safety and proper handling are critical in a knifemaking environment. The warning, "The arbor was part of the spindle so be careful," underscores this point. An arbor is a shaft or spindle on which a cutting tool or grinding wheel is mounted. If the arbor is integrated directly into the spindle, it means less flexibility for replacement or adjustment, and any damage to the arbor could compromise the entire spindle, leading to costly repairs or dangerous operating conditions. This level of attention to detail and awareness of machinery specifics is characteristic of experienced knifemakers who understand that the quality of their tools directly impacts the quality and safety of their output.
Maintaining precision tools, understanding their mechanics, and prioritizing safety are not just best practices; they are fundamental to the art and business of crafting durable, functional, and beautiful knives.
Valuing Blades: The Economics of Custom and Heirloom Knives
Determining the price of a custom knife, especially fixed blade knives, is a complex process that goes far beyond the cost of raw materials. For those just entering the custom knife market, whether as buyers or aspiring makers, questions about pricing are inevitable. As one might ponder, "As someone who is just beginning this journey, I have some questions regarding the pricing of custom knives, particularly fixed blade." This query opens up a fascinating discussion on the economics of artisan crafts.
At its core, the principle is simple: "Economics 101 dictates that something is worth." What is it worth? It's worth what someone is willing to pay for it, balanced against the cost of production and the maker's desired profit. However, for custom knives, "worth" is multifaceted. It includes:
- Material Costs: High-quality steels (e.g., CPM-S35VN, Damascus), exotic handle materials (e.g., stabilized wood, mammoth ivory, carbon fiber), and premium hardware contribute significantly.
- Labor and Skill: The countless hours spent on design, forging, grinding, heat treating, finishing, and sharpening. A master knifemaker's time is valuable due to their acquired skill and reputation.
- Tools and Overhead: The investment in specialized machinery (grinders, ovens, etching equipment), workshop space, utilities, and consumables.
- Design and Innovation: Unique designs, intricate patterns, and innovative features add to the knife's appeal and value.
- Maker's Reputation and Demand: Established makers with long waiting lists can command higher prices due to their proven track record and the exclusivity of their work.
- Market Trends: Like any market, knife prices can be influenced by current trends, collector interest in specific styles, or the availability of certain materials.
For custom fixed blades, the absence of moving parts often means a focus on robust construction, ergonomic handle design, and superior edge retention, all of which contribute to the final price. The value isn't just in the utility but in the artistry and the story behind the blade, a factor that certainly applies to unique items like "Jacobs Ladder knives."
Restoring Heirlooms: A Delicate Craft
Beyond new custom pieces, there's a significant market for the repair and restoration of heirloom knives, which often carry immense sentimental and historical value. The desire to preserve these pieces is strong, even if they are in poor condition. For example, the query about restoring a specific model highlights this need: "I am also looking for an Oregon knifemaker to repair/restore an heirloom Remington R1123 pocketknife."
Such knives, despite their age or condition, can be quite valuable. As noted, "It is a pretty valuable knife but in fairly rough condition and I would like to." The value here isn't just monetary; it's often tied to family history, personal memories, or the historical significance of the piece itself. Restoring an heirloom requires a specialized skill set, as it involves not just repairing damage but also preserving the knife's original character and historical integrity.
A reputable restorer will assess the knife's condition, identify the appropriate materials and techniques to use (e.g., matching original handle materials, carefully cleaning and polishing without over-grinding, repairing broken springs or blades), and provide an estimate. The process is a delicate balance between repair and preservation, ensuring that the knife can continue its legacy for generations to come. Finding the right expert, particularly for a specific region like Oregon, is crucial for such a sensitive and valuable task.
Navigating the Knife Market: Tips for Collectors and Enthusiasts
Whether you're a seasoned collector or just starting to appreciate the art of blades, navigating the knife market requires knowledge, patience, and a keen eye. The journey, as Joshua Jacobs's early experience highlights, often begins with a degree of "uneducation about knives." Overcoming this involves active learning and engaging with the community.
For those interested in custom knives, including unique pieces like "Jacobs Ladder knives," or even restoring heirlooms, here are some tips:
Where to Find Reputable Knife Makers and Information
- Knife Shows and Expos: These events are invaluable for meeting makers in person, handling different knives, and learning directly from experts. You can see the craftsmanship up close and discuss custom orders.
- Online Forums and Communities: Reputable knife forums (e.g., BladeForums.com, KnifeDogs.com) are excellent resources for discussions, reviews, and direct interaction with makers and experienced collectors. They often have dedicated sections for custom knives and maker profiles.
- Professional Organizations: Associations like the Knifemakers' Guild or the American Bladesmith Society set standards for craftsmanship and often list their members, providing a directory of skilled artisans.
- Specialized Dealers and Retailers: High-end knife retailers often carry custom pieces and can provide expertise and authentication. They act as a trusted intermediary between makers and buyers.
- Social Media (with caution): Platforms like Instagram and Facebook are popular for makers to showcase their work. However, always verify the maker's reputation and legitimacy before making commitments.
- Books and Magazines: Traditional print media still offers in-depth articles, historical context, and maker profiles that can deepen your understanding of the craft.
Always prioritize clear communication with makers, especially for custom orders or restorations. Ask about materials, lead times, and payment terms. For heirloom pieces, ensure the restorer has specific experience with similar knives and can provide references or examples of their work. Education is your best tool in ensuring a satisfying experience in the world of custom blades.
The Enduring Appeal of Handcrafted Blades
The journey into the world of knives, from understanding the legacy of families like the Jacobs and their "Jacobs Ladder knives" to appreciating the intricate processes of blade making and restoration, reveals a craft rich in history, skill, and passion. It's a world where functional utility meets artistic expression, where steel and handle materials are transformed into objects of both practicality and beauty.
The appeal of handcrafted blades lies not just in their sharpness or durability, but in the story they tell – of the maker's
Related Resources:
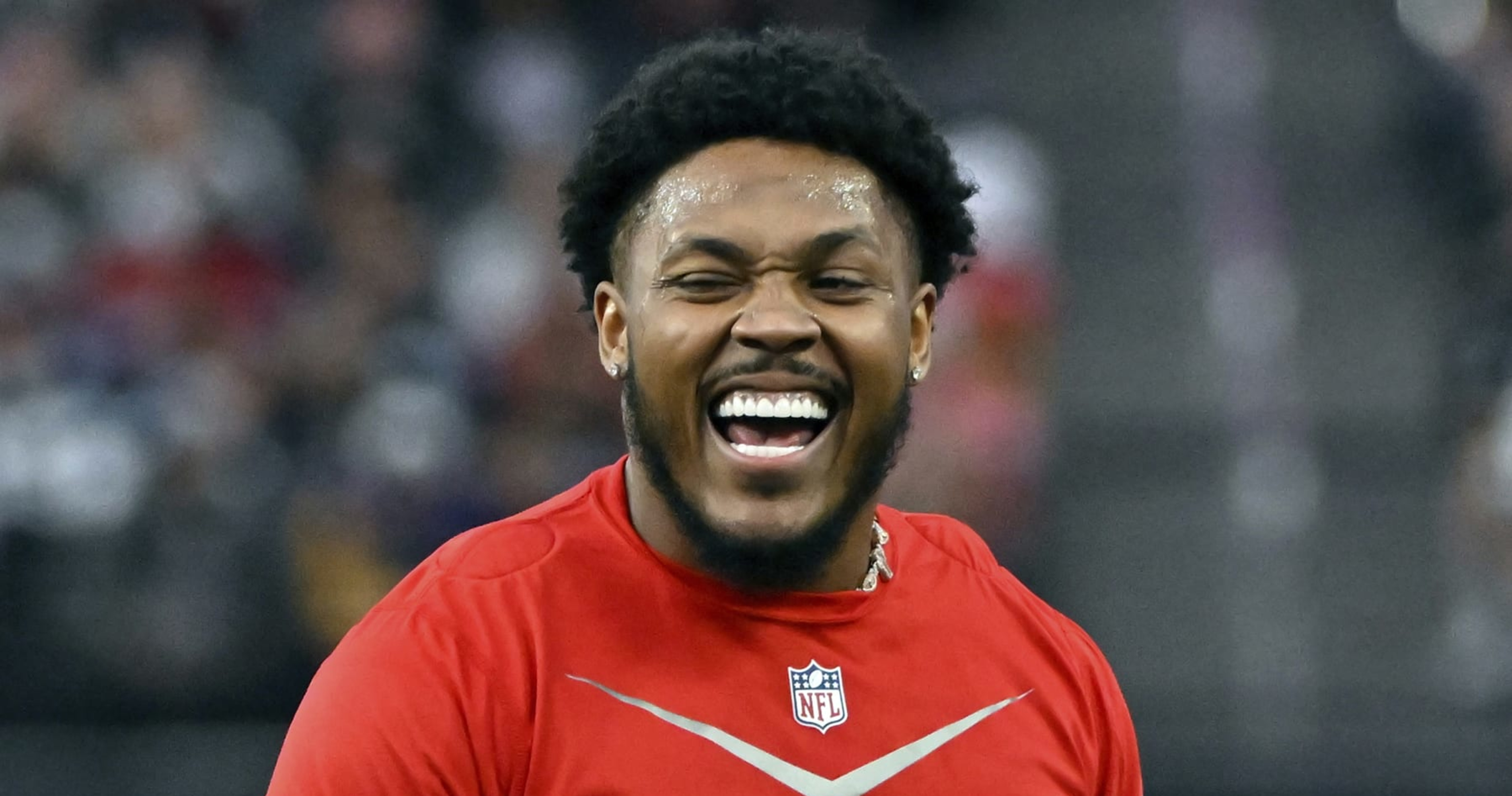
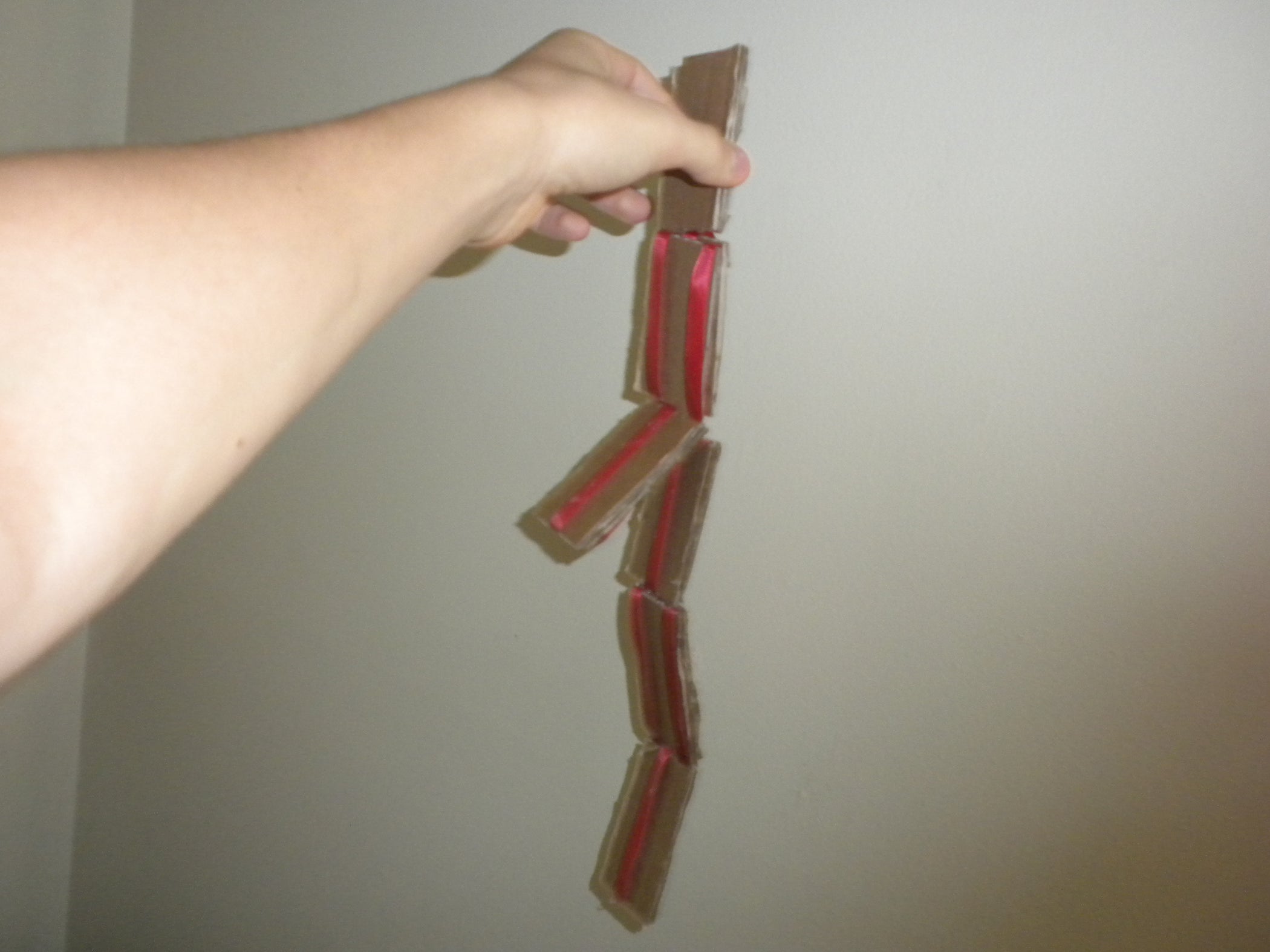
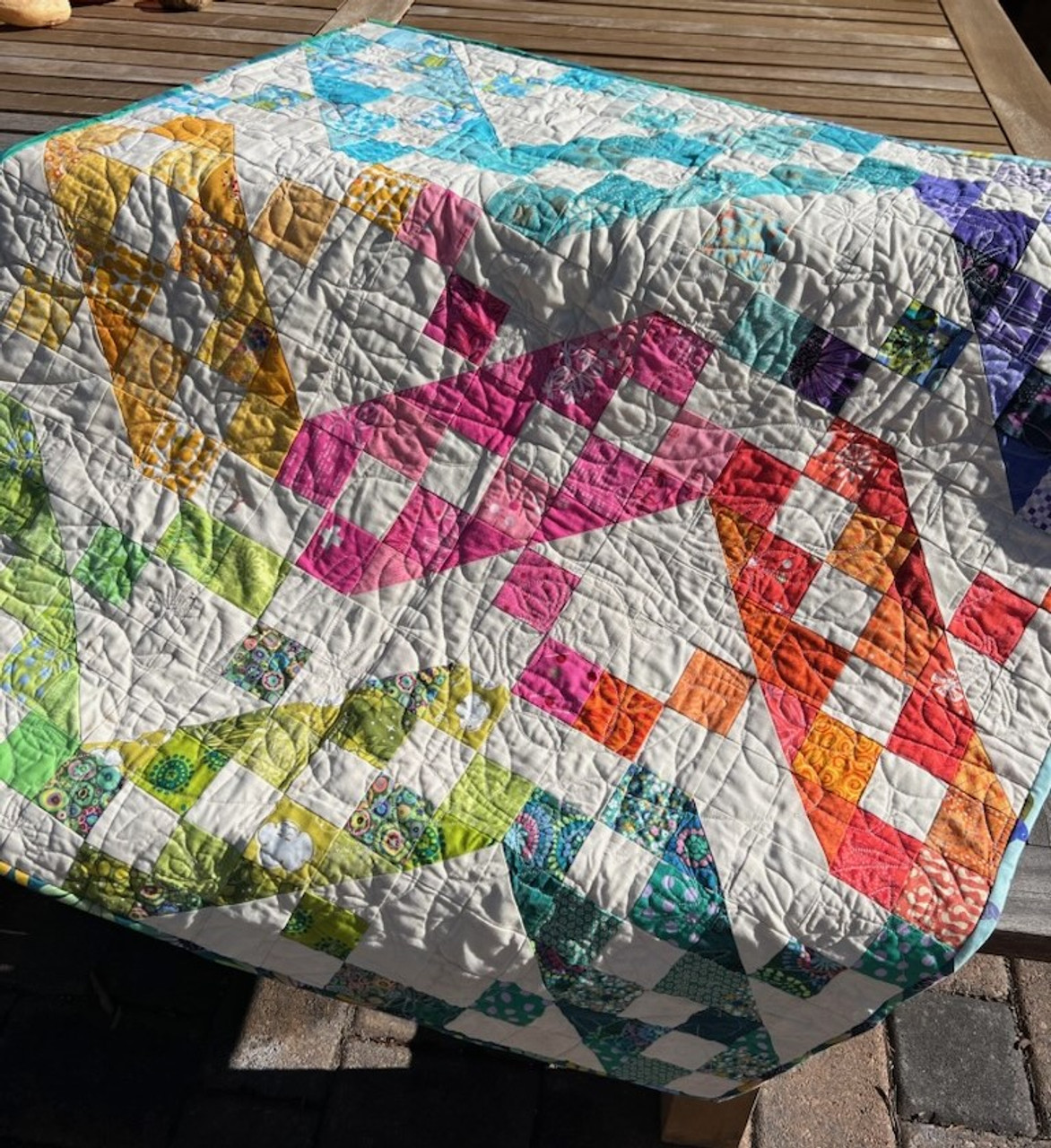
Detail Author:
- Name : Martine Zulauf Sr.
- Username : littel.juston
- Email : rohan.faye@gmail.com
- Birthdate : 1995-02-15
- Address : 299 Eloisa Lake Apt. 705 Cassieshire, HI 93218
- Phone : 1-920-392-1903
- Company : Kozey, Glover and Kassulke
- Job : Computer Systems Analyst
- Bio : Nihil voluptatem non est ex voluptatum. Explicabo ex ea et quam itaque optio. Tempora quod omnis sit pariatur tempore.
Socials
twitter:
- url : https://twitter.com/maida1136
- username : maida1136
- bio : Aut ullam commodi cum. Impedit distinctio et voluptatem. Quam officia eligendi optio a quia sapiente.
- followers : 2533
- following : 2054
facebook:
- url : https://facebook.com/maida.carroll
- username : maida.carroll
- bio : Consequatur in rem possimus dolorum sed.
- followers : 746
- following : 85
instagram:
- url : https://instagram.com/maida_carroll
- username : maida_carroll
- bio : Voluptatibus vero tempore occaecati perferendis. Quo ipsam modi culpa enim corrupti.
- followers : 2457
- following : 625
tiktok:
- url : https://tiktok.com/@mcarroll
- username : mcarroll
- bio : Sunt quasi aut accusamus voluptatem tempora ut qui.
- followers : 5345
- following : 583
linkedin:
- url : https://linkedin.com/in/mcarroll
- username : mcarroll
- bio : Dolorem sed unde quidem.
- followers : 3467
- following : 1881